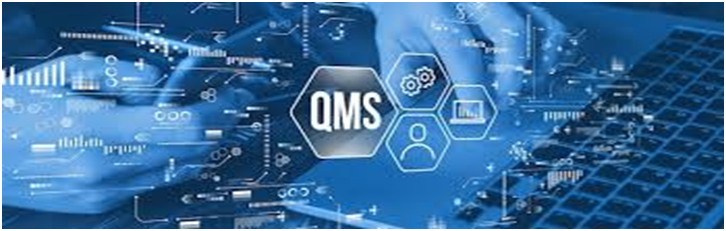
A quality management system (QMS) is a collection of business processes and procedures which aims to ensure that the quality of products or services meets – or exceeds – customer expectations. Such systems are typically repeatable and measurable, and rely on continuous improvement.
Types of quality management systems
There are many different types of quality management systems, each with their own advantages and disadvantages. Some of the most common ones are:
Standardised systems:
These rely on established standards and follow agreed codes and regulations. Examples include ISO certifications such as ISO 9001. To pass the ISO standards, a business needs to satisfy all the requirements relating to quality and documentation, as well as audits. ISO certification is voluntary for most businesses. However, it may be a legal or contractual requirement in certain sectors and industries.
Total quality management (TQM)
TQM is a management framework that relies on continuous, organisation-wide efforts to ensure long-term customer loyalty and success. It places a strong focus on process measurement and controls as means of continuous improvement.
Continuous quality improvement
This system, also known as CQI, focuses on continual incremental improvements, rather than processes and functions. The emphasis is on teams and individuals, and their importance in ensuring the quality of products and services. One of the most popular continuous improvement tools is a four-step quality model, the Plan-Do-Check-Act (PDCA) cycle.
Six Sigma
This is a data-driven methodology that focuses on process improvement. Under this approach, the processes are defined, measured, analysed, improved and controlled to achieve maximum quality. See more on Six Sigma.
Core elements of quality management systems
At their core, most quality systems will have several key elements:
- quality policy
- quality objectives
- quality manual
- quality procedures, instructions, and records
- document control
- organisational structure and responsibilities
- data management
- processes
- customer satisfaction
- continuous improvement
Put together, these elements make up a system which defines expectations, responsibilities and actions needed to achieve the expected quality of products or services.
- Quality Policy:
quality policy sets the top-level objective of your QMS, from which all other objectives flow. When properly crafted and communicated, your quality policy changes the culture of your business. It aligns every member of your team to a unified goal.
- Quality Objectives:
Quality objectives are measurable goals related to the value of a company’s products, services and processes. These come from the International Organization for Standardization (ISO ) quality management systems, which is a set of guidelines to help organizations meet their customers’ needs and requirements.
- Quality Manual:
A quality manual is a document that states the company’s intentions for operating and executing the processes within its quality management system. It can include policies for all areas of the business that affect your ability to make high-quality products and meet your customers and ISO’s requirements.
- Quality Procedure:
The purpose of a QMS procedure is to create product and service consistency by mapping out the steps required to perform a specific process. Businesses using a quality management system need to create standard procedures to ensure the process is completed in line with best practices every time.
- Document Control:
Document control can be defined as a series of practices that ensure that documents are created, reviewed, distributed, and disposed of in an organized and verifiable manner. You might also use the term “document management”. While these terms are closely related, they are not interchangeable.
- Organisational Structure and Responsibilities:
Develop and make available to all employees a list of key personnel and their job descriptions, responsibilities, along with an organizational chart of key employees as they relate to the QMS. This should effectively define, document, and communicate the organizational structure of the QMS.
- Data Management:
Data quality management is a set of practices that aim at maintaining a high quality of information. It goes all the way from the acquisition of data and the implementation of advanced data processes to an effective distribution of data.
- Customer Satisfaction:
Customer satisfaction is essential to the success of the organization. It is a key indicator of organizational monitoring. In the quality management system according to IATF 16949, customer satisfaction has a remarkably high priority.
- Continous Improvement:
A process in which a company focuses on constantly improving its products, services, and processes is known as continuous quality management improvement.